THANK YOU FOR SUBSCRIBING
Editor's Pick (1 - 4 of 8)

The ABC of Manufacturing Digitalization
Brandon Lee, Director of Product Strategy & Commercialisation, Intech APAC Chair, Smart Automation Industry Group, Singapore Manufacturing Federation

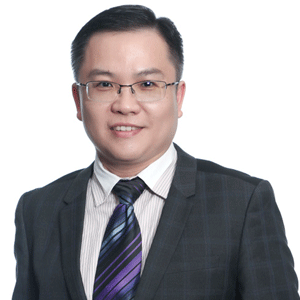
Brandon Lee, Director of Product Strategy & Commercialisation, Intech APAC Chair, Smart Automation Industry Group, Singapore Manufacturing Federation
Changes is defined as the intended and unintended changes that we encountered in manufacturing. Intended Changes are those that provide positive values to our business, things like modifying spec to support different processes, dynamic scheduling to improve asset utilization, Just- In-Time inventory control to improve inventory turn, etc. The more such activities are done correctly, the more benefits we can realize. Therefore, one of the objectives of digitalization is to expose these opportunities in runtime so that actions can be taken quickly to realize the maximum benefits. Unintended changes are those that negatively impact our business if happened, for example, unscheduled breakdown of equipment, reworks and defect, excessive waiting time for resources, etc. Detections events would not be sufficient so a key digitalization objective is to identify and control the factors that lead to these events so that interventions can be executed to prevent the incidents. Collecting KPIs (key performance indexes) and KPVs (key process variables) against event context for generating alerts with first-line reporting will allow these events to be integrated into manufacturing activities for achieving better efficiency. This is the primary aim of “Connectedness” with IIoT and edge olution.
The last part of the puzzle is on the business values that can be generated from managing the Changes. There are many levels of using the data to create business value, starting from providing visibility to understand the problem, connecting and coordinating the actions, predicting the issues and prescribing the solution, and finally adapting to the changes automatically with potential self-adjustment and self-learning via AI. Each level of digitalization maturity can trigger a round of business process re-engineering that could potentially offer a major upgrade to the manufacturing capabilities. The net result of many rounds of these activities would be the strengthening of the manufacturing DNA that eventually enables the manufacturers to bring unparallel service to the market, something we often call disruption. I can’t stress enough of the importance of this because the whole idea of Industry 4.0 is to create a new experience with better options, starting from the end user perspectives and propagate throughout the whole supply chain. The “new” way of using data to manage the manufacturing activities can create the multiplier effect if coupled with the right use of advanced automation technology like robotics, AGV, ASRS, Drones, etc The opposite of this is also true in a sense that if we limit the growth of our digitalization maturity, the use of the corresponding advanced technology will also be limited or in some case, produce negative impact to the business if it fails to handle the changes.
As a concluding note, many people look at manufacturing digitalization as a technological upgrade exercise by replacing/upgrading resources used in manufacturing activities. I strongly encourage them to relook again on their strategy, focus instead on the value of digitalization in creating a better experience for their customers and their eco-system. It feels great to talk about creating a factory of the future but it is even greater to harvest the value of digitalization and orchestrate an awesome experience of the future.
Check out: The Manufacturing Outlook
Weekly Brief
I agree We use cookies on this website to enhance your user experience. By clicking any link on this page you are giving your consent for us to set cookies. More info
Read Also
