THANK YOU FOR SUBSCRIBING

Five Trends for Manufacturing's Fourth Wave
François Barbier, President of Global Operations and Components, Flex

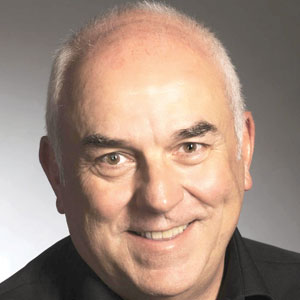
François Barbier, President of Global Operations and Components, Flex
As traditional product categories today are replaced by new lines of business, companies too, are radically changing their production methods.
These firms have learnt to embrace Industry 4.0, a term coined in 2011 by Henning Kagermann, the head of the German Academy of Science and Engineering. On the back of the first industrial revolution which occurred in the late 1700s, the second during the early 20th century, and the third after World War II, the new fourth wave is powered by advancements that include smart manufacturing, robotics, artificial intelligence, and the Internet of Things (IoT).
Concurrently, this shift will drive the need for smart automation further, says François Barbier, president of Global Operations and Components at Flex, a Sketch-to-Scale® solutions provider. Flex is no stranger to how companies are adopting IoT solutions. “Think about what we’ve seen over the last 150 years with the three industrial revolutions. Everything is now produced better, faster, and with higher quality,” says Barbier. “Compare the first car to the cars we have right now. That higher quality drives more demand, more consumption, more work for people, and more work in the world.”
Global brands like Epson, General Motors, IBM, Intel, Lockheed Martin, and Microsoft are all investing in making their manufacturing more intelligent.
“Our ways of designing products and getting information from customers have changed dramatically. The data that informs how we design our products can be much more or much less prescriptive depending on the customer,” says Barbier.
Flex, he noted, still has traditional customers who are very prescriptive like Cisco, HP, and Nokia, which detail everything they want, including product design. Flex then offers these companies the service of making those products and materials, and delivers those products to customers. “But now we have a new set of customers coming to us with a sketch of a product idea. They’re asking Flex to design it. For us, this is driving a need for new ways of working and processes in the manufacturing space.”
So what skills should manufacturing leaders possess to find success in Industry 4.0?
1. Seeing Around Corners—in 360°
New tools are allowing companies such as Ford Motor Company and BAE Systems to create and test situations in the virtual world.
Each of these two companies have been experimenting with virtual reality (VR) technology—Ford, to stimulate how people interact with their vehicles, while BAE Systems has adopted it for planning the construction of submarines.
2. Viewing the Fourth Wave —in 3-D
Also making a mark in the manufacturing world is 3-D printing, which allows for the seamless creation of tangible products using a single machine. Barbier says that this is “a fundamental change, because if you’re adding material, that gives you a lot more possibilities for how you design the part.
“For a certain category of product where you would normally need six pieces, 3-D printing can achieve the same thing in one piece without any additional processes like welding or screwing.”
Three-dimensional printing can also reduce waste by recycling plastic and cut down on the wait time for replacement parts and transportation. Its implications for mass production are varied, making advancements possible in products ranging from toys to medical devices.
In addition to these consolidation and scrap benefits, additive manufacturing also offers many other benefits, including precision material placement, significant time and cost savings, and the ability to decentralize the manufacturing of basic parts by providing services closer to end markets.
The data that informs how we design our products can be much more or much less prescriptive depending on the customer
These benefits allow for a vertically-integrated supply chain in Flex’s operations.
3. Advanced Manufacturing -- on Autopilot
Automation is another vital aspect of the industry’s future. According to Barbier, a significant portion of Flex’s manufacturing processes are already fully automated.
For Flex, automation means creating products with the kind of accuracy and stamina that humans can’t provide and doing so in environments that would be considered unsafe for humans. The new generation of robotics is not only much easier to program, but is also more user-friendly than ever and, with such capabilities as voice or image recognition, can work with humans and re-create complex human tasks. These plug-and-play type of robots “are becoming easier to use and much more collaborative,” says Barbier.
“Robots are just going to do what you ask them to do—nothing more, nothing less. Right now, a lot of new technologies are based on tactical sensors, optical sensors or X-ray sensors. These things are preventing accidents because the robots are able to see, or sense, if I’m touching it and know to stop. The good news is now we can increasingly integrate robotics into production lines alongside human beings.” These human-machine interfaces, or HMIs, provide feedback on worker safety and simple performance issues. New robots that are more agile, skilled, cheaper, and safer could decrease labor costs.
4. Building Intelligent Factories—in the Cloud
Beyond robotics, AR, and VR, factories are becoming more savvy with cloud computing and smart sensors, retrofitting older equipment with the latter and installing them in newer machines.
“If you think about any process in the manufacturing environment, there are many barometers you need to manage to have a process that delivers the right value-add you’re looking for,” says Barbier.
“What we call ‘smart’ or ‘IoT’ is just one of those barometers that you need delivered on a real-time basis.” He notes that the IoT allows us to get the right information at the right time to make the right decisions, likening it to a speedometer that shows how fast you’re driving in the moment instead of your speed from the day before.
Barbier believes that “deep” data is what matters most, noting that simply “capturing information without doing anything is meaningless. It’s very important to gather a lot of data, but it’s more important to have the right data to take the right action.” Deep data could uncover consumer insights that create an increase in regional manufacturing. It can also connect multiple factories by region, share movable assets, and reduce time and waste.
5. Robots on the Rise— Managed by Humans
Building a better manufacturing sector with augmented and virtual reality, robotics, and data analysis using smart equipment naturally raises an important question: What will the Industry 4.0 workforce look like?
While there are still some significant challenges ahead, the outlook is strong in spite of the obvious concern of robots stealing jobs. “The vast majority of automation technology will not outright replace humans; instead, it will simply make their work more efficient,” wrote Jim Rock, the CEO of the vision-guide industrial vehicle company Seegrid.
“That new demand will ensure that the more-competitive American companies of the future will continue to thrive -- even if the world looks different than it does today.”
Barbier agrees, noting that the bulk of automation is used for work that would be considered unsafe, too imprecise, or simply impossible for humans to perform, such as those that involve toxic fumes, extreme temperatures, or that demand an acute level of precision.
This makes robots a complement to, not a replacement for, human workers. Because of robots, “we’ll be able to increase our output,” he says. “The jobs that are going to be taken over by automation are actually going to be replaced with additional product volume and categories. We will need people who are able to manage these new operations, manage the robotics, to program them and maintain them. People who used to produce things with their hands, they’ll start to produce things with their brains. You’ll have to take care of the information that you’re going to get out of this automated equipment and interpret what you can do with that information. I believe there are lot of different categories of experts and skilled people we’ll need for designing, building, and using the automation.”
Designing useful algorithms and software that capture, process, interpret, and predict information is key to success in the digital manufacturing age. Flex is already utilizing these kinds of complex tools to inform procedures in the U.S. and abroad. It’s a change that will necessitate new kinds of training and educational programs, but as the IoT has already been influencing enterprise in fields such as medicine and business, it’s not hard to imagine that the manufacturers of the future will readily prepare workers for the challenges ahead.