THANK YOU FOR SUBSCRIBING
Editor's Pick (1 - 4 of 8)

A Smart Manufacturing Call to Arms
Rhett Ramos, Director, Asia IT, Allegro MicroSystems Philippines

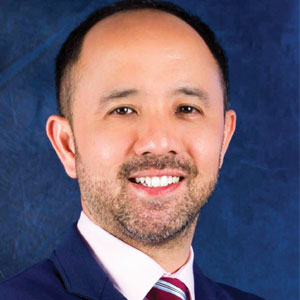
Rhett Ramos, Director, Asia IT, Allegro MicroSystems Philippines
Many say we are now facing the fourth industrial revolution where cyber-physical, transparent data exchange between systems and machines, and autonomous decision-making are propagating on not only the factory floor but also the entire supply chain